The schematic, shown below, of a single use CIP Set shows the balance (buffer) tank, typically of the order of 200 litres and associated pumps, valves and pipework.
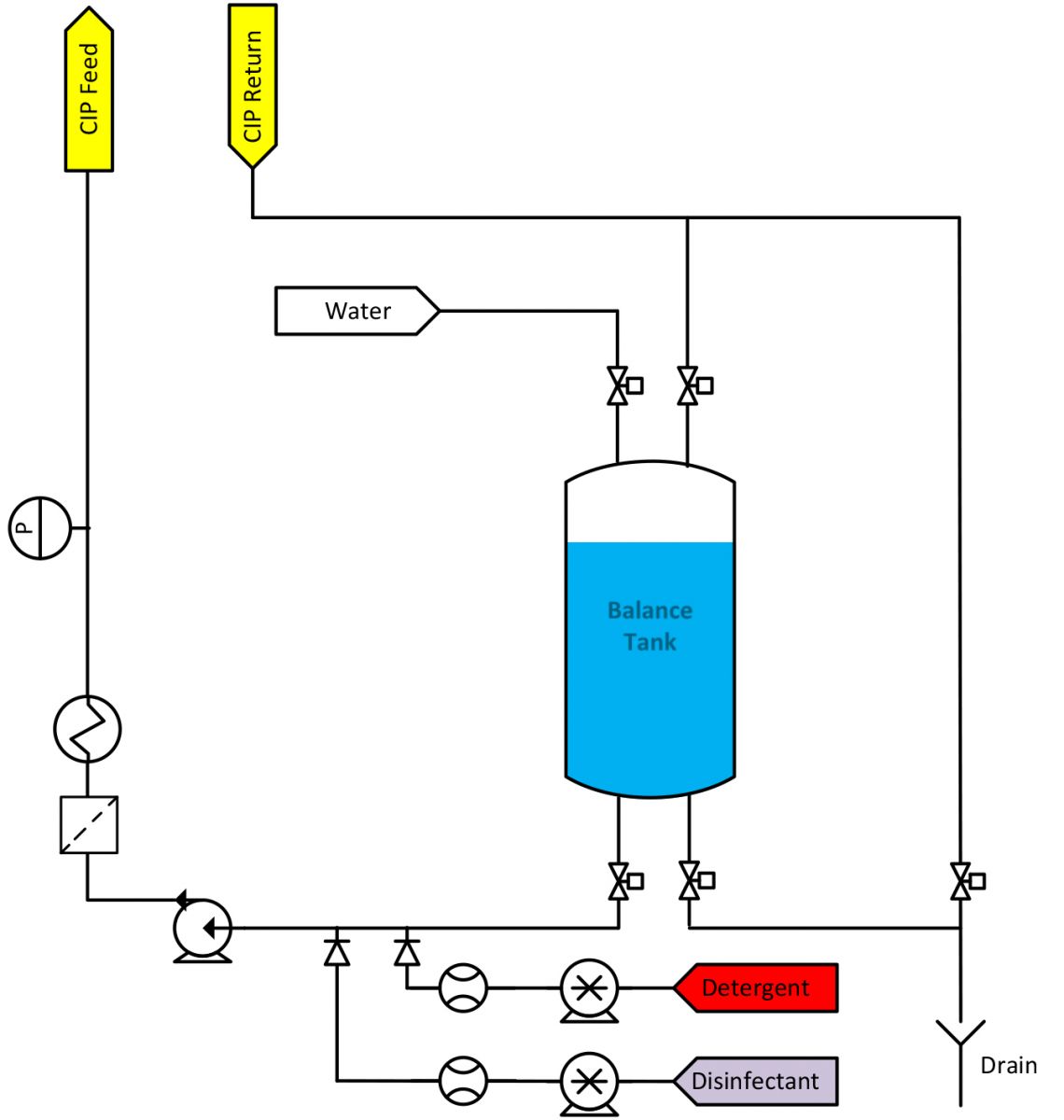
Single Use CIP Set - typical cleaning cycle
Prerinse Feed clean water to vessel for 5 mins.
Return to drain.
Detergent Feed clean water to vessel
Return to balance tank.
When circuit made run caustic dosing pump for given volume.
Plate heat exchanger or direct steam injection used to heat solution.
Allow to recirculate for 20 mins.
Drain down vessel and balance tank.
Rinse Feed clean water to vessel for 5 mins.
Return to drain.
Disinfect Feed clean water to vessel
Return to balance tank.
When circuit made run disinfectant dosing pump for given volume.
Allow to recirculate for 5 mins.
Drain Drain system and balance tank.